Table of contents
Key Takeaways
- The global pandemic has exposed single points of failure across the supply chain.
- Pharmaceutical supply chains must become agile to adapt to the “next normal”
- Collaborative issue management is essential to prevent supply chain disruptions.
By John Bermudez | April 24, 2020
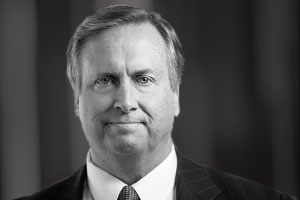
This April marks 50 years since the ill-fated—but ultimately “successful”—voyage of the Apollo 13 spacecraft. Like the current crisis, survival required fast thinking, teamwork, and real-time data to address a life-threatening situation. Today, the pharmaceutical industry is facing an “Apollo 13 moment” of its own—and the need for a more agile supply chain has never been more apparent.
The COVID-19 pandemic has pointed to single points of failure such as API sources from a single nation or sources of supply that are thousands of miles from finished goods production or where drugs are dispensed. In the weeks and months ahead, the pharmaceutical industry will be taking stock of the lessons learned during this pandemic—and where, why, and how it exposed critical weaknesses in its supply chain.
To avoid the risk of a critical supplier going offline, pharma companies will need to set up secondary, “near-shore,” or in-country sources of supply. In fact, this may be mandated by government agencies if pharmaceutical companies don’t do it first. Whether this is done in advance or in the midst of an emergency, the pharma industry has a significant hurdle: new manufacturing processes must be validated. This means, as new sources of supply are set up, issues will surface that must be resolved quickly to get these new suppliers online and to achieve validated status.
Tomorrow’s supply chain: More diverse, more complex, and more agile
As you bring new sources of supply online, your supply chain complexity will also increase. Companies must analyze their internal operations to see if their people, processes, and systems are agile enough to identify, onboard, and manage secondary sources of critical materials and to integrate them quickly into their existing supply chains. For many, however, a reliance on “four-wall” processes and legacy systems have left them with:
- No single source of visibility for identifying and managing supply chain issues;
- No organized supply chain partner collaboration and no coordinated approach for issue resolution;
- Data in unstructured, non-digital formats, exchanged between a few individuals, and;
- Ad-hoc processes that don’t support continual process improvement.
To maintain the continuous flow of materials and finished goods—even in a crisis—your manufacturing and distribution operations must be able to access to the most current and accurate information; follow up immediately when issues and disruptions arise; collaborate in real time with supply chain partners to resolve issues; and implement process improvements to ensure that your supply chain is resilient enough to overcome unexpected disruptions.
Collaborative issue management: Results built on relationships
As I noted in my last blog post, a digital supply network can provide the collaborative platform required for end-to-end supply chain agility. To achieve a best-in-class, efficient supply chain with on-time in-full product delivery, you will also need to establish a collaborative issue management process that:
- Eliminates silos of internal and external information,
- Enables direct collaboration between internal and external teams,
- Provides a uniform data structure and eliminates ad hoc document sharing,
- Supports real-time problem escalation and resolution, and;
- Prevents recurrent issues through continual process improvement.
Like NASA’s Mission Control center, collaborative issue management leverages the collective expertise from customers, suppliers, and service providers to find the right solution as quickly as possible. By engaging internal organizations and external partners in a shared issue resolution process, companies can also leverage a full spectrum of historical data to support process improvement methodologies. In doing so, we can be sure that the lessons learned during a global crisis like COVID-19 can be studied and applied to create a more safe, secure, and reliable pharmaceutical supply chain.
John Bermudez is the General Manager, Digital Network Platform, at TraceLink. He is responsible for leading the overall strategy, business planning, and operational execution for TraceLink’s Digital Network Platform business.
Return to: The Patient-Driven Supply Network