800 total articles
Filter
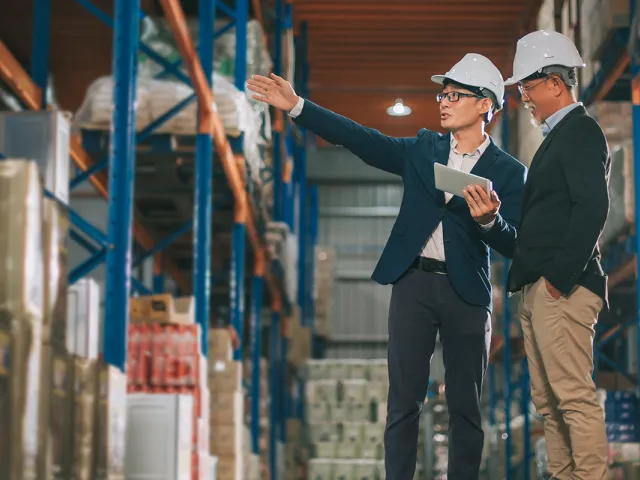
Video
From Manual Processes to Intelligent Orchestration: How Nutra-Med Packaging Is Advancing Supply Chain Digitalization
View More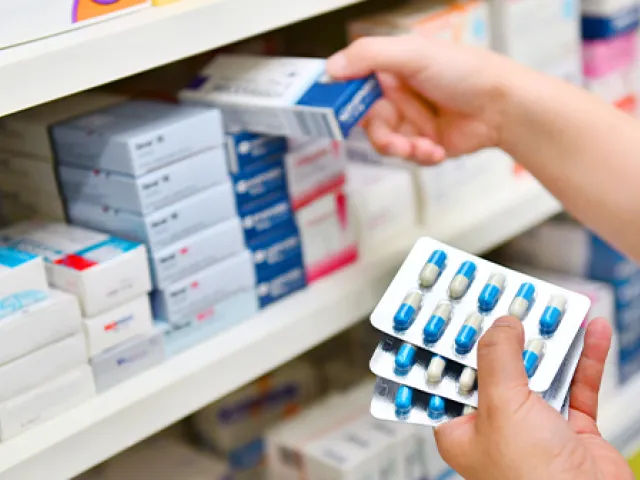
Video
Improving Invoice Visibility and Reconciliation with Suppliers Across DSCSA Networks
View More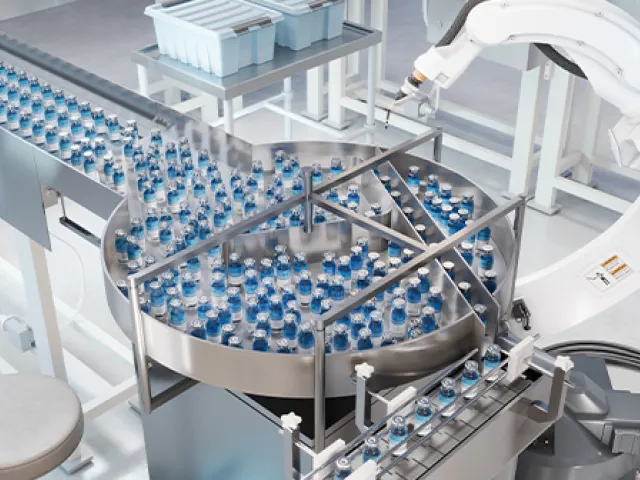
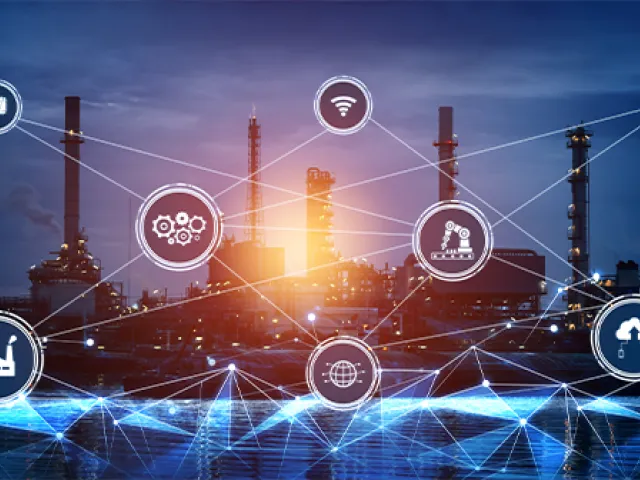
Video
Accelerating Supply Chain Digitalization: How TraceLink Simplifies Partner Onboarding
View More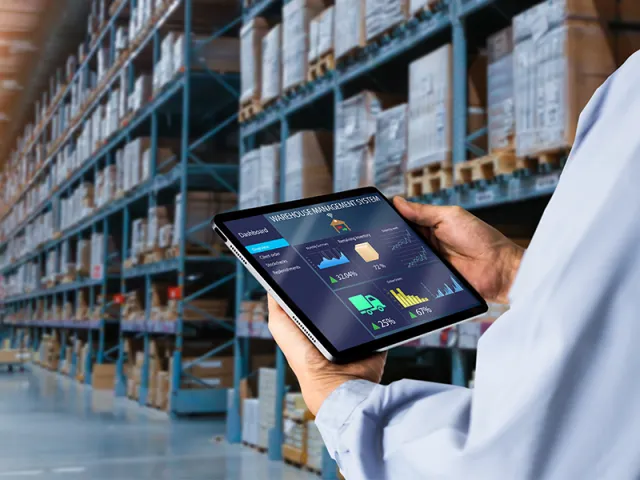
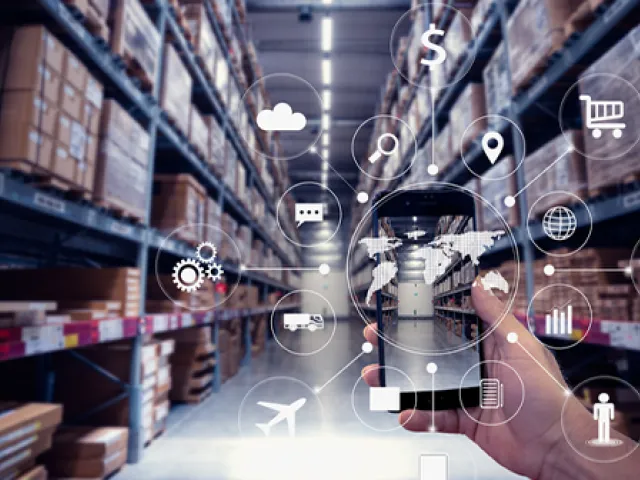
Video
Serialization + Digitalization Data + AI/ML Can Balance Supply Chain Efficiency with Customer Service
View More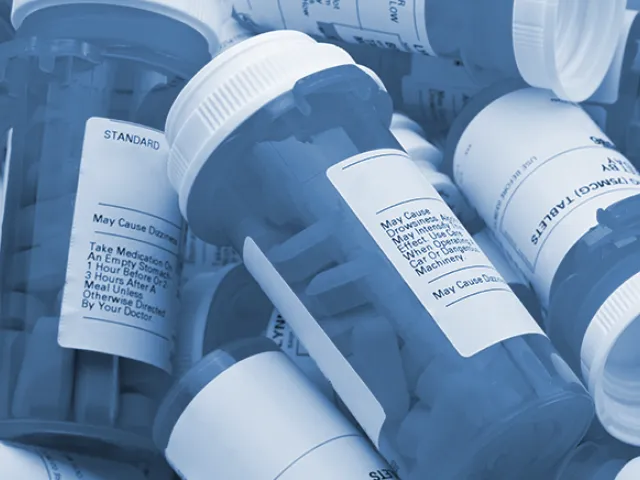
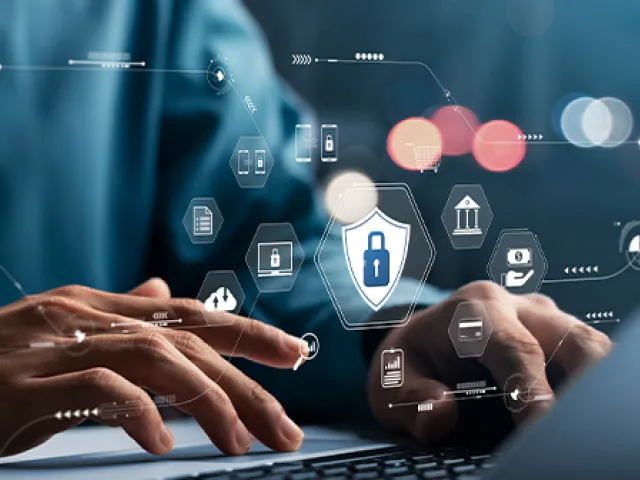
Blog
Life Sciences and Healthcare Supply Chain Leaders Achieve DSCSA Readiness with TraceLink
View More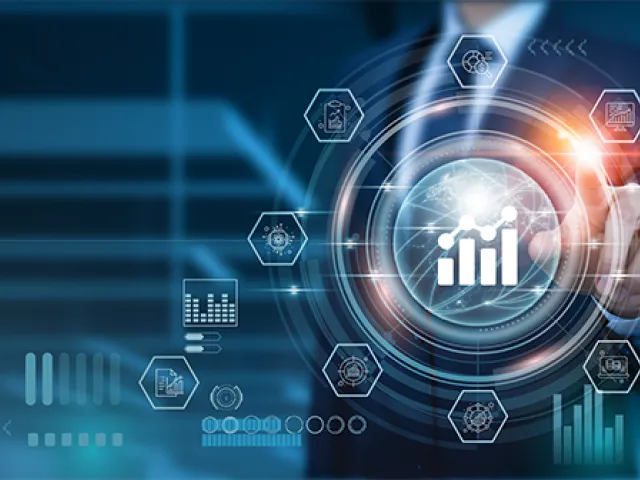
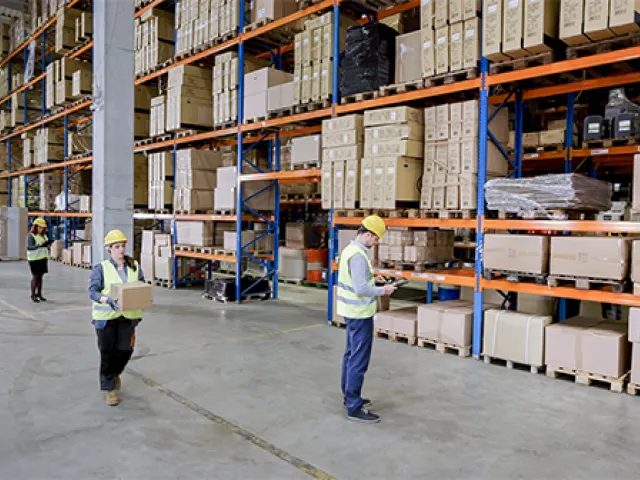
Video
Why Digital Innovation in Healthcare Logistics is Critical for Today's Efficient, Agile, and Sustainable Supply Chain
View More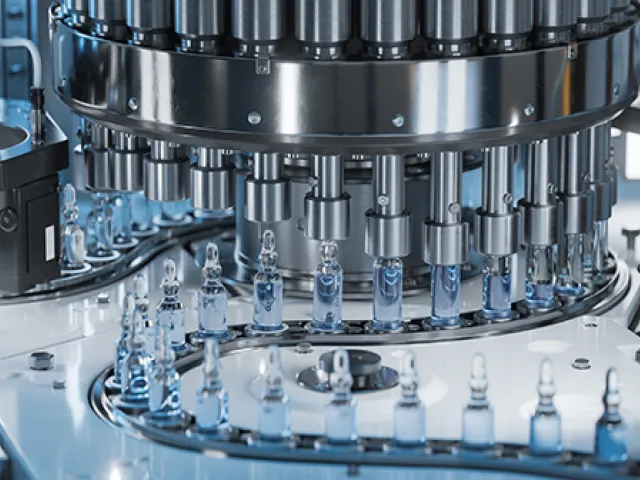
Video
DSCSA Compliance Exceptions: Learnings and Responses from Early Adopters and Their Network Partners
View More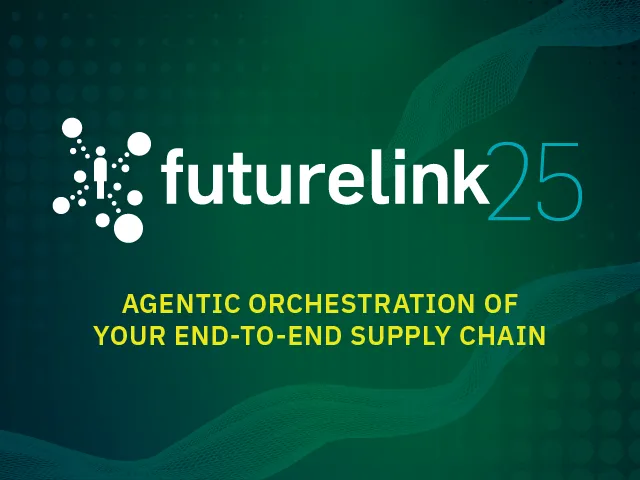
Blog
Meet the Visionaries Shaping the Future of the Life Sciences Supply Chain at FutureLink Barcelona 2025
View More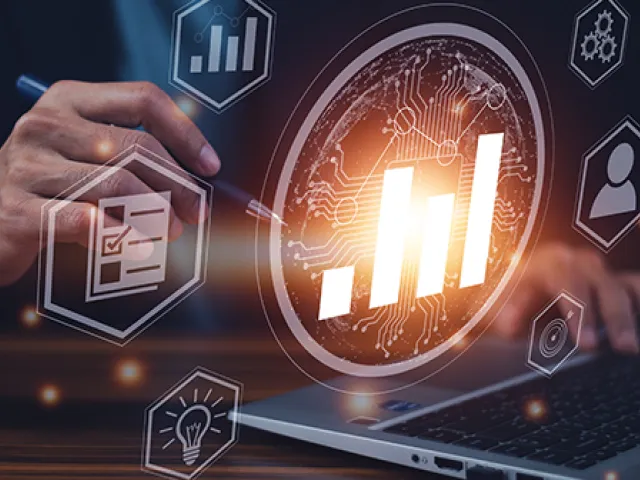
Video
Insights on DSCSA Distribution and Logistics Operational Excellence as a Foundation for Digitalization
View More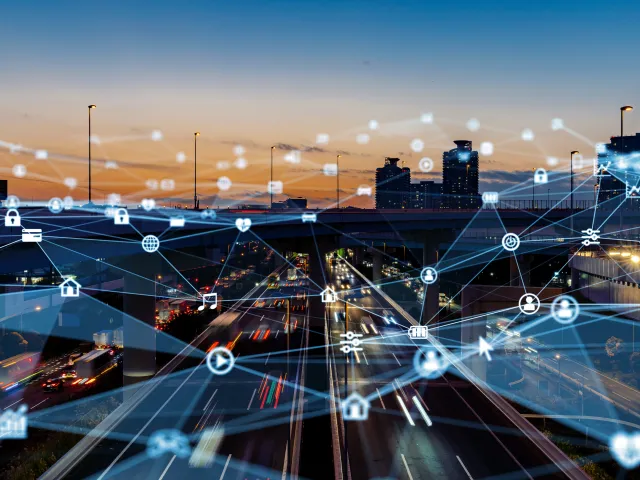
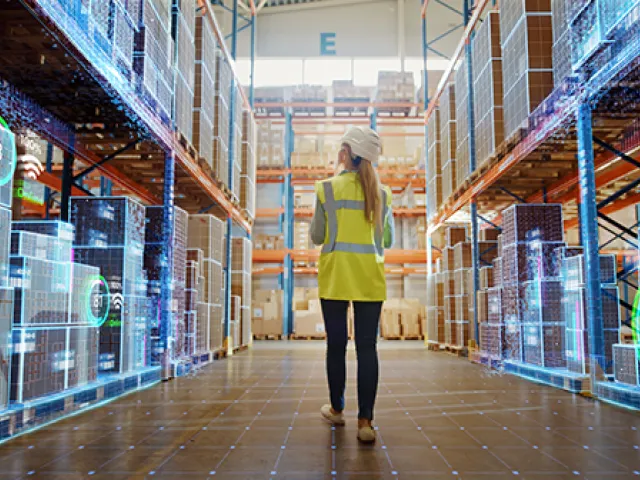
Video
Integrated Serialized Product Distribution Systems for Customer Service and Operational Efficiency
View More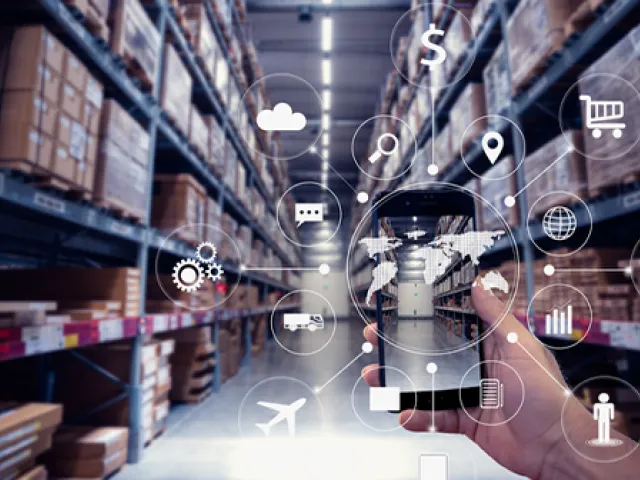
Video
Improve Supply Planning and Inventory Management with Supply Chain Intelligence Powered by DSCSA EPCIS Data
View More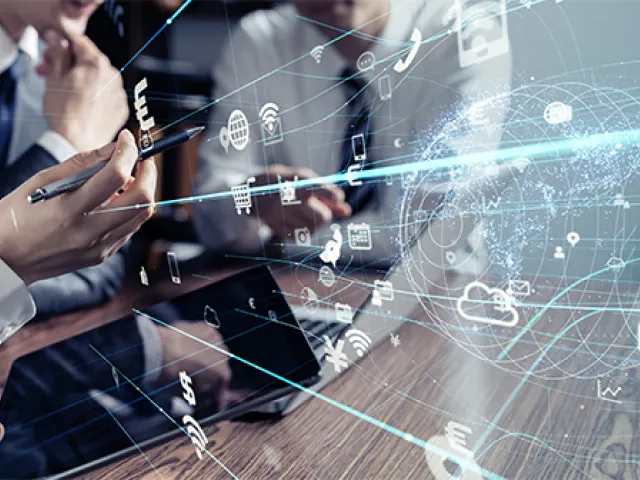
Video
Reverse Logistics (Returns) Reconciliation Using Serialized Product and Business Transaction Data
View More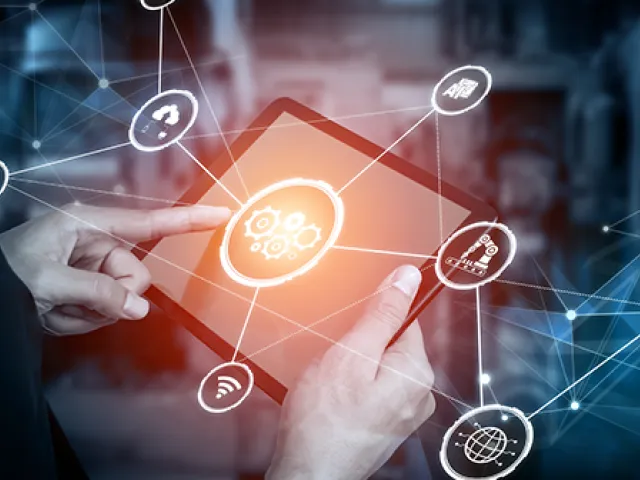
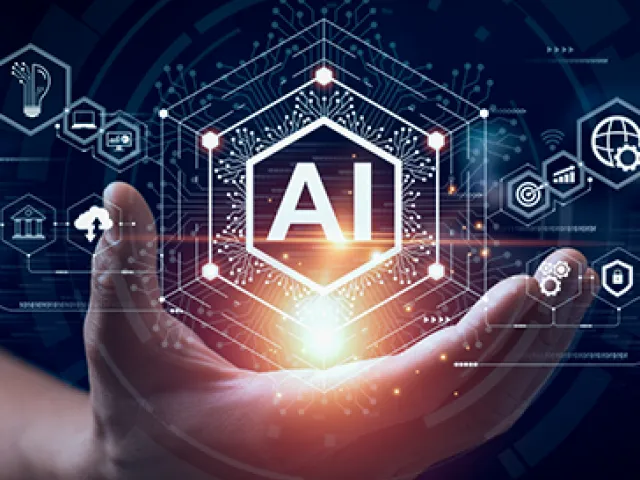
Video
Unlocking the Power of GenAI: How TraceLink is Enhancing Supply Chain Intelligence - Inside and Out
View More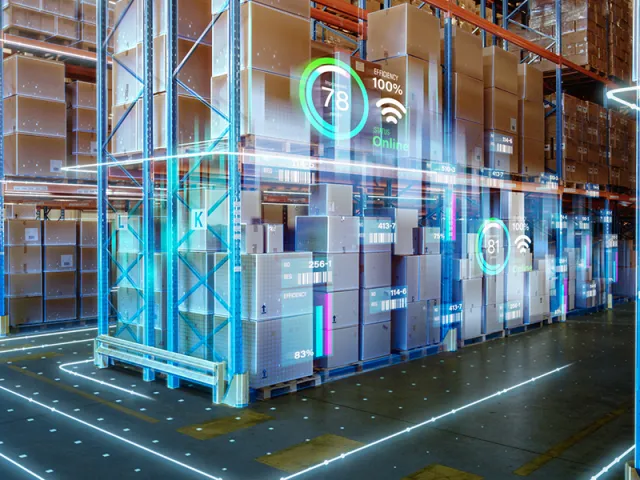
Video
Digitalizing Targeted Recall Notices for Real-Time Matching with DSCSA EPCIS Shipment Data
View More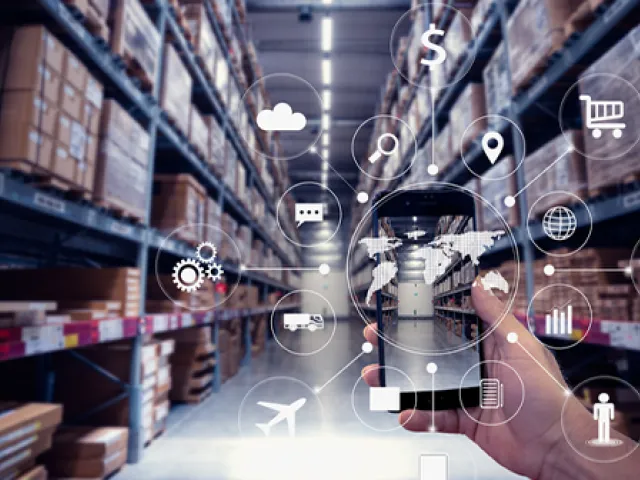
Video
Optimize Working Capital by Orchestrating Serialized Product Inventory Transactions and ASNs with Network Partners
View More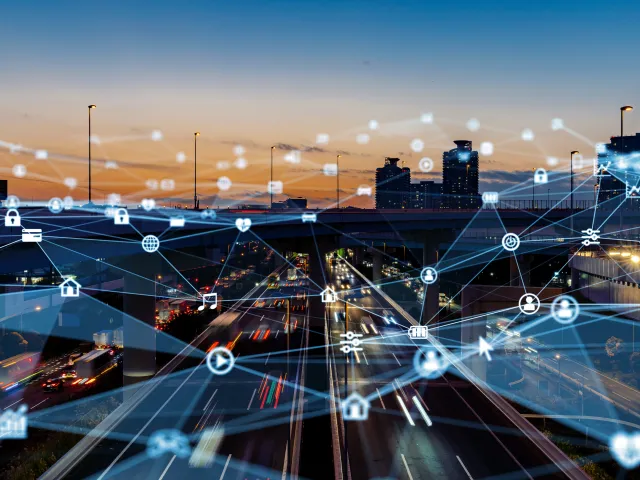
Video
Breaking Silos: Creating the Collaborative Corporate Foundation to Enable Supply Chain Orchestration
View More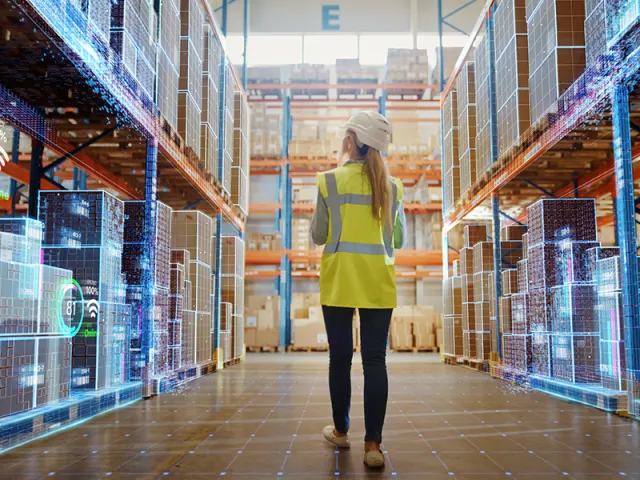
Video
Improve Chargeback Reconciliation With EPCIS, Serialized Product Data, and ASN and PO Transactions
View More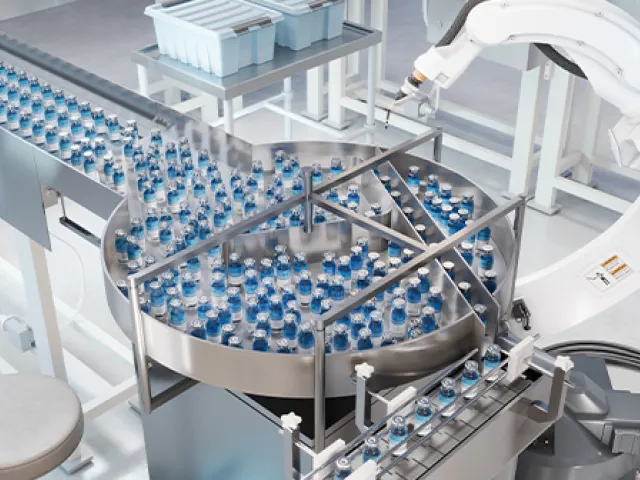
Video
Driving Business Predictability and Strategic Partnerships in CMO Networks by Leveraging DSCSA and Digitalization
View More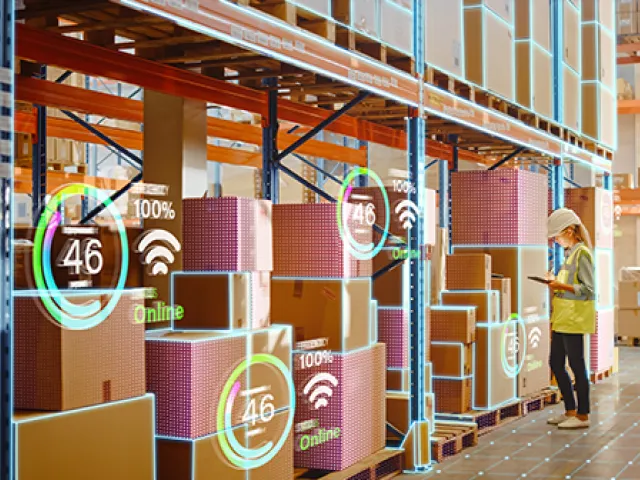
Video
Build Upon DSCSA to Digitalize and Automate Procure-to-Pay for Lead-Time, Cost, and Inventory Reduction
View More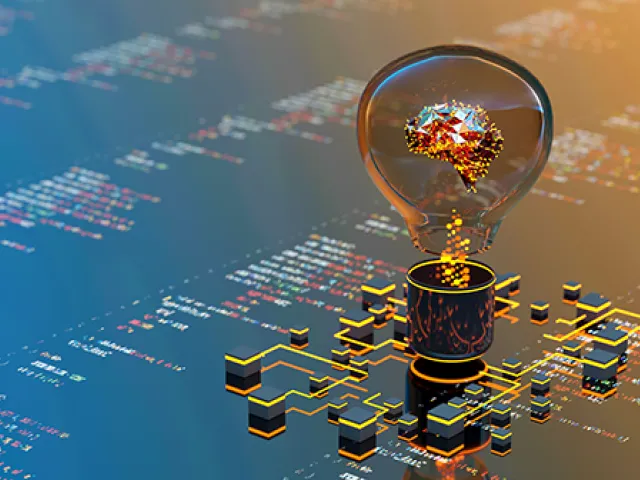
Video
Yes, Digitalized POs & ASNs Can Drive Strategic Impact for Manufacturers & Contract Packagers
View More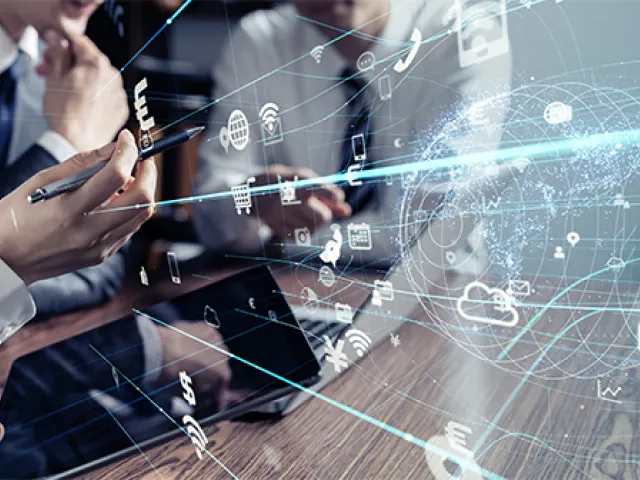
Featured Webinars
How Leading Pharma Manufacturers are Accelerating Commercialization and Cutting Waste with Genpact, Kinaxis, and TraceLink
View More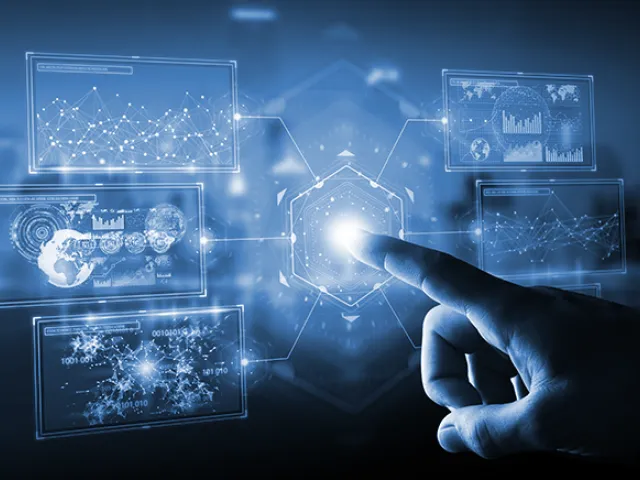
Video
Overheard at FutureLink Boston 2025: 7 Key Takeaways from TraceLink CEO Shabbir Dahod’s Vision for the Future of Supply Chains in Life Sciences
View More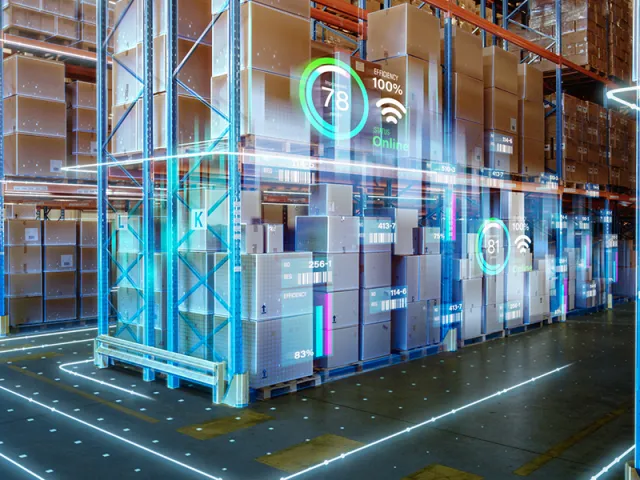
Video
Improving Planning and Forecast Effectiveness by Feeding Supply Chain Planning with Digital Inventory and Order Data
View More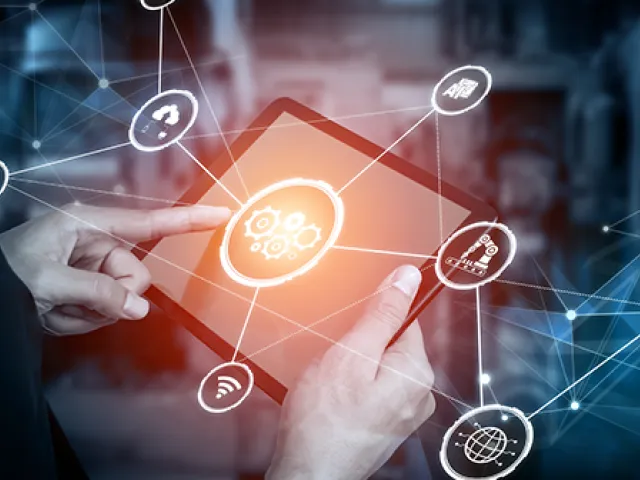
Video