806 total articles
Filter
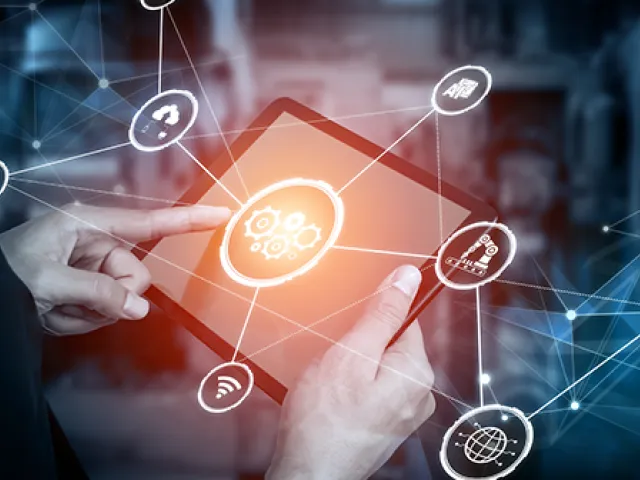
Blog
Eliminate Manual and Error-Prone Forecasting and Planning: TraceLink MINT Links All Your Customers Without Custom Integrations
View More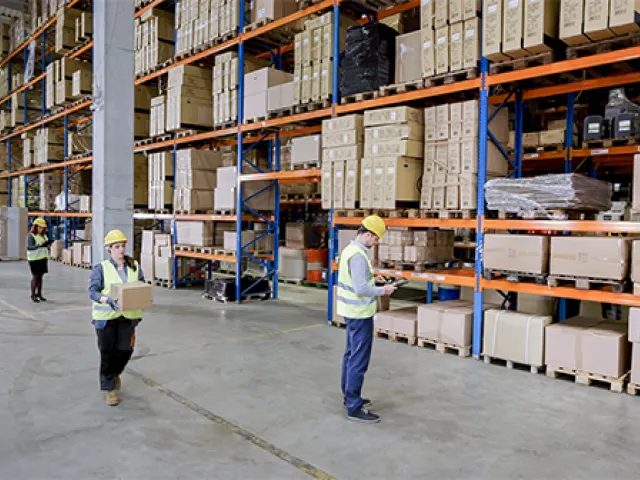
Video
Building a Safer, Smarter Life Sciences and Healthcare Supply Chain: A Wholesale Distributor’s View on MINT
View More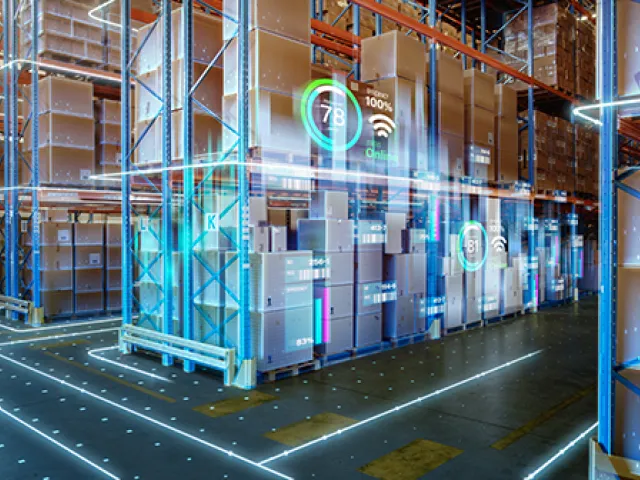
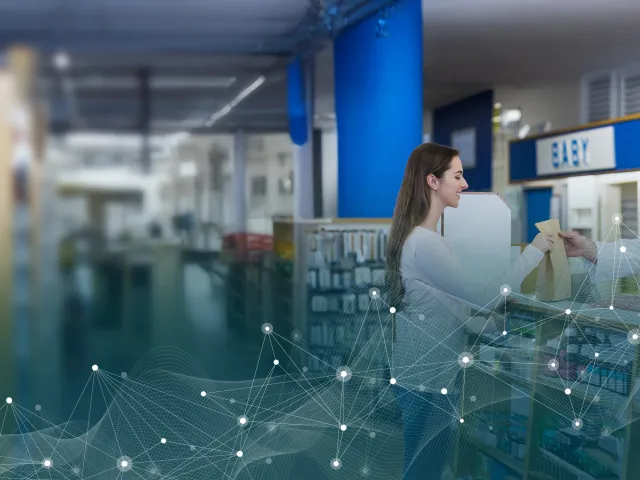
Video
Boston Medical Center Streamlines Invoice Management and Unlocks Supplier Discounts with MINT for Commerce
View More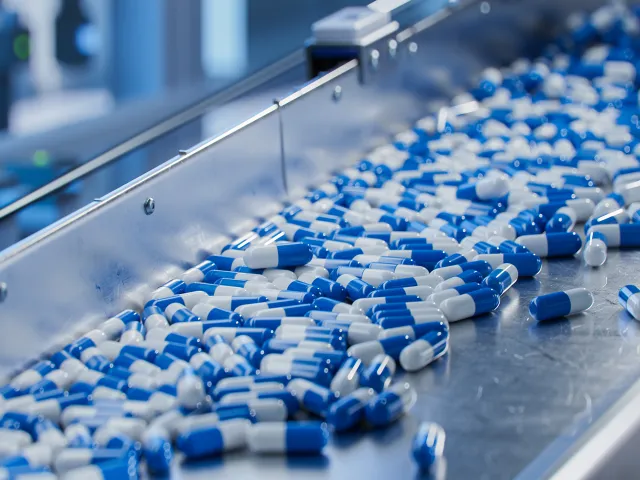
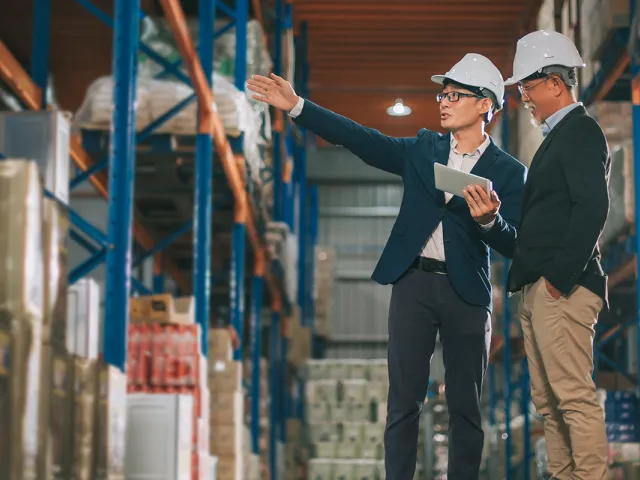
Video
From Manual Processes to Intelligent Orchestration: How Nutra-Med Packaging Is Advancing Supply Chain Digitalization
View More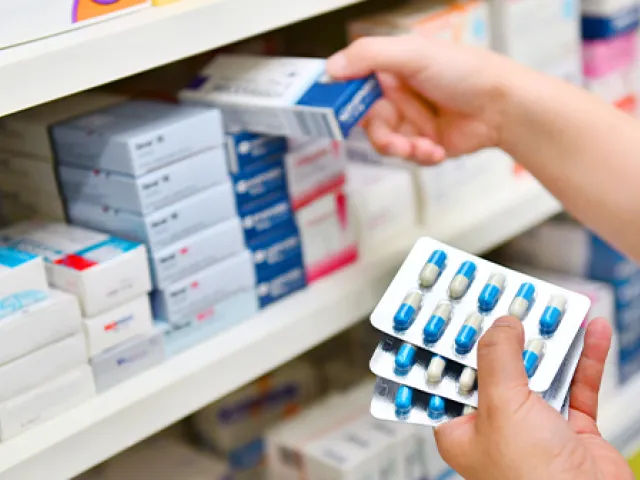
Video
Improving Invoice Visibility and Reconciliation with Suppliers Across DSCSA Networks
View More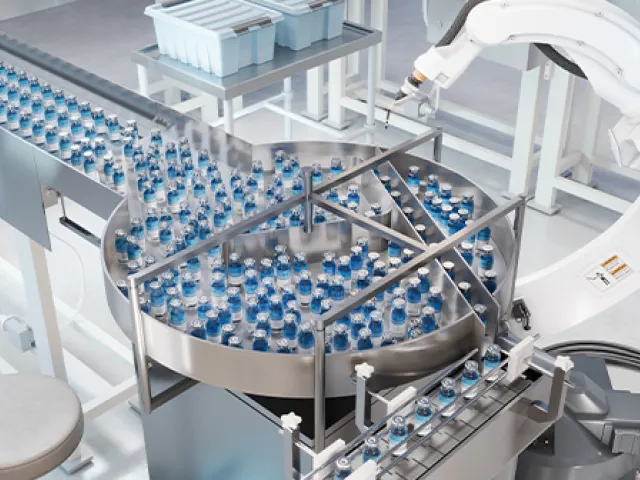
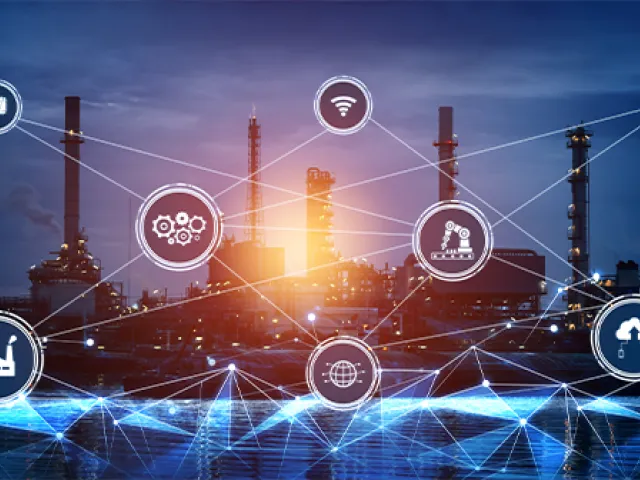
Video
Accelerating Supply Chain Digitalization: How TraceLink Simplifies Partner Onboarding
View More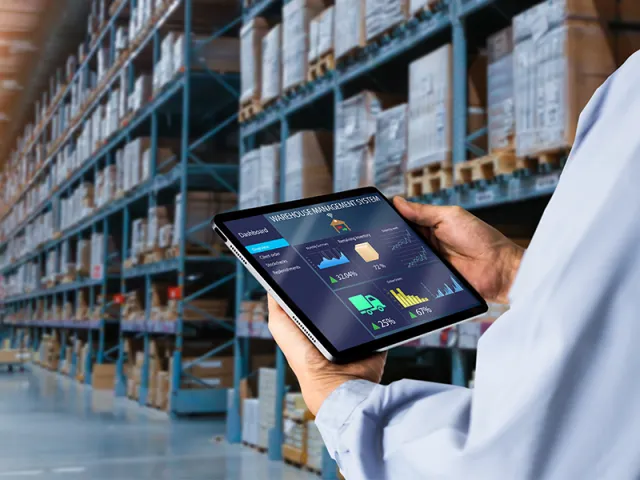
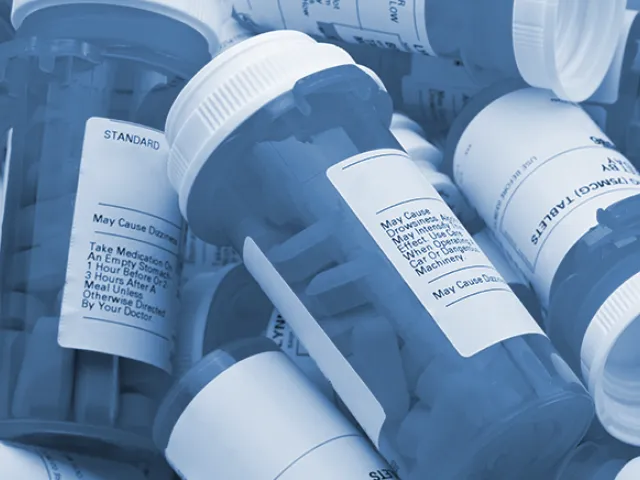
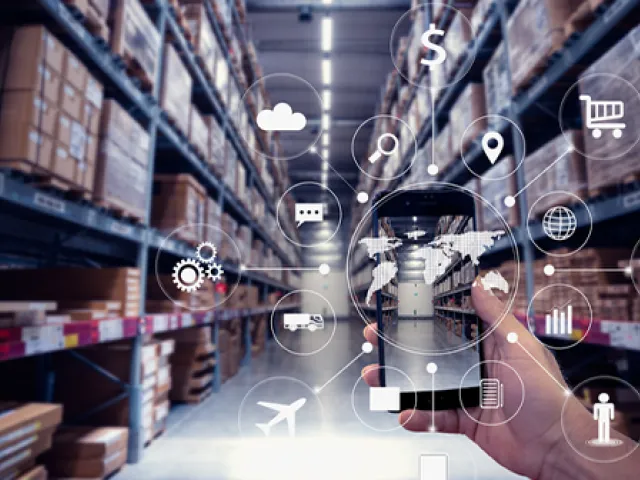
Video
Serialization + Digitalization Data + AI/ML Can Balance Supply Chain Efficiency with Customer Service
View More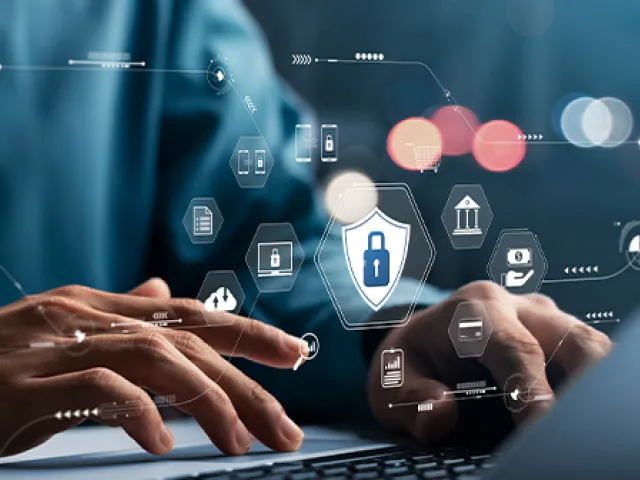
Blog
Life Sciences and Healthcare Supply Chain Leaders Achieve DSCSA Readiness with TraceLink
View More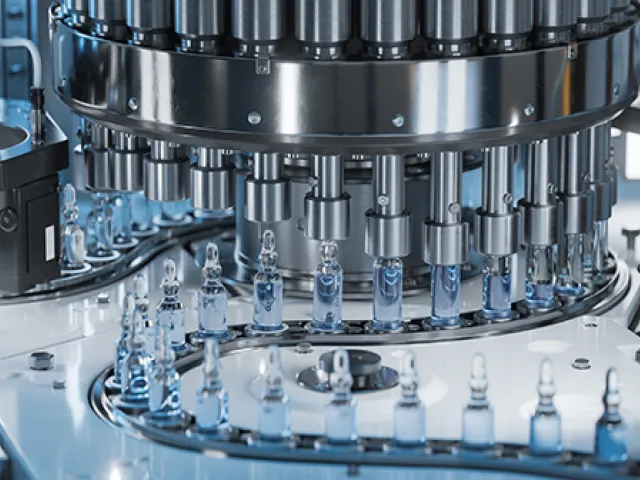
Video
DSCSA Compliance Exceptions: Learnings and Responses from Early Adopters and Their Network Partners
View More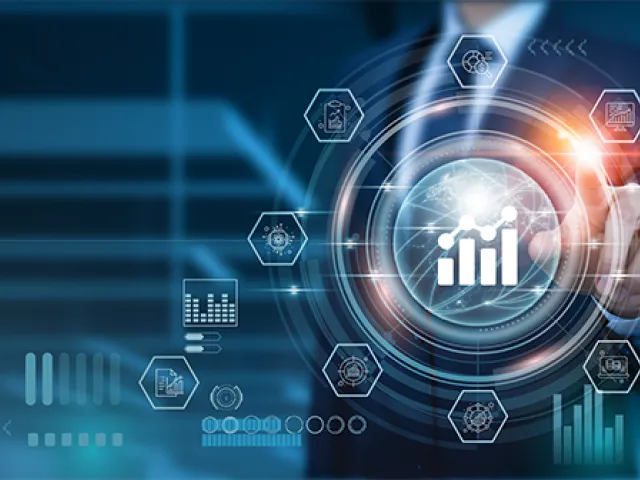
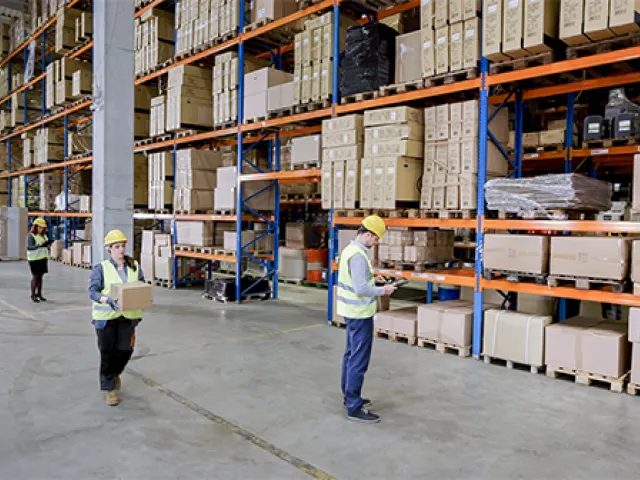
Video
Why Digital Innovation in Healthcare Logistics is Critical for Today's Efficient, Agile, and Sustainable Supply Chain
View More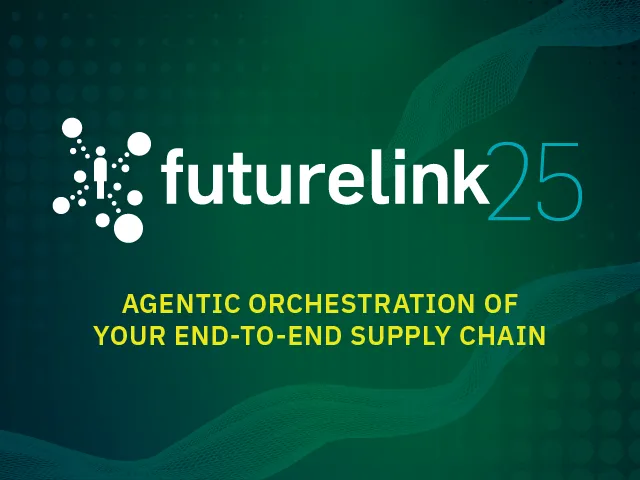
Blog
Meet the Visionaries Shaping the Future of the Life Sciences Supply Chain at FutureLink Barcelona 2025
View More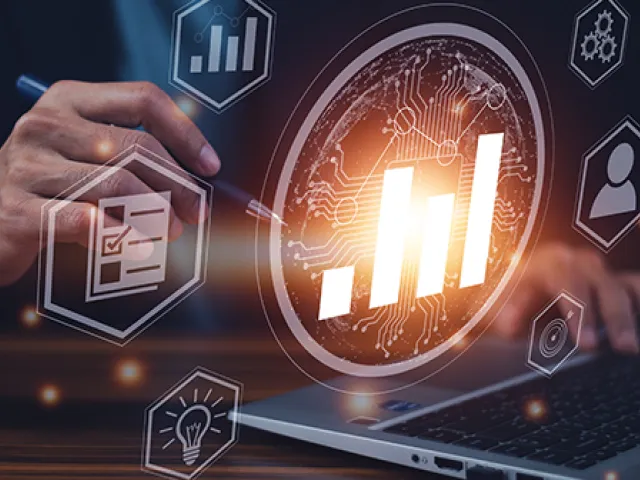
Video
Insights on DSCSA Distribution and Logistics Operational Excellence as a Foundation for Digitalization
View More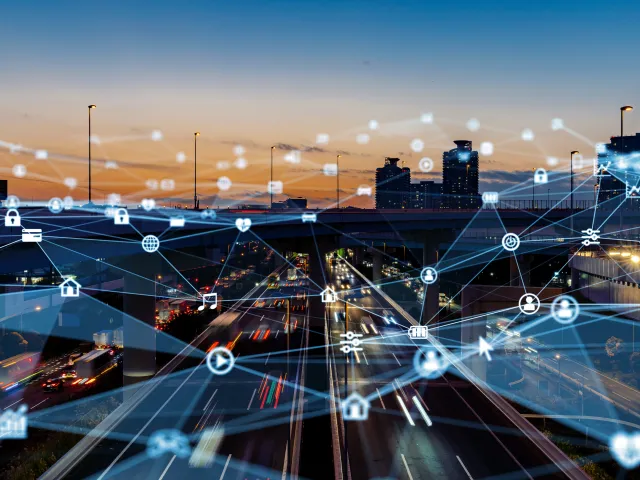
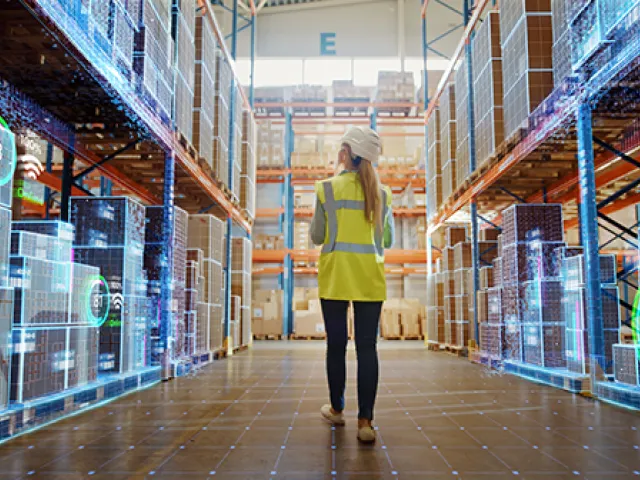
Video
Integrated Serialized Product Distribution Systems for Customer Service and Operational Efficiency
View More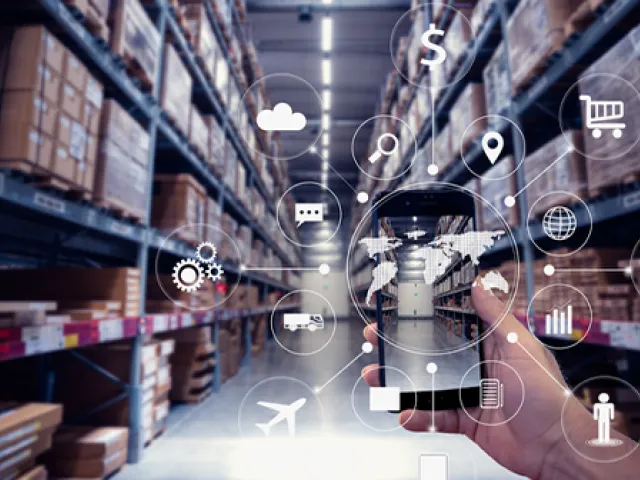
Video
Improve Supply Planning and Inventory Management with Supply Chain Intelligence Powered by DSCSA EPCIS Data
View More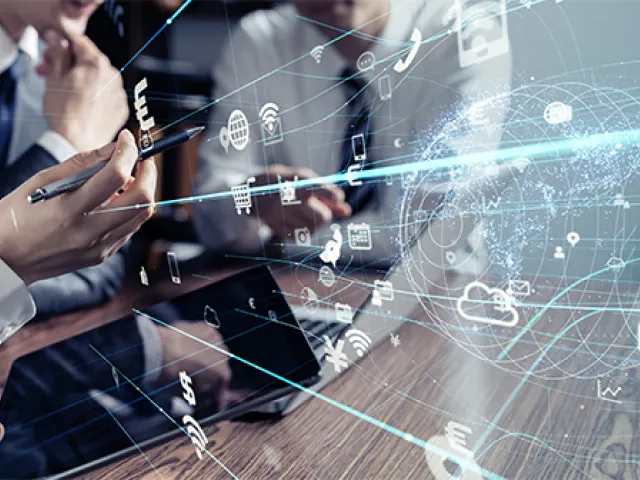
Video
Reverse Logistics (Returns) Reconciliation Using Serialized Product and Business Transaction Data
View More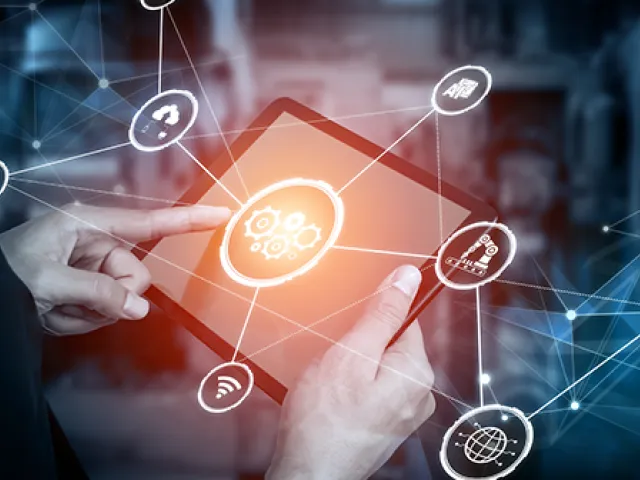
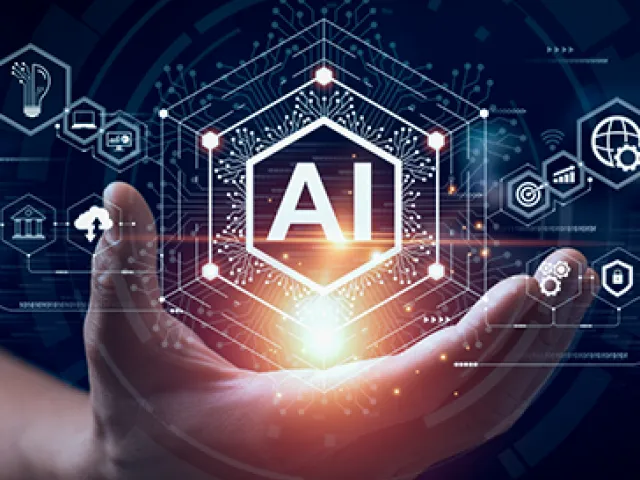
Video
Unlocking the Power of GenAI: How TraceLink is Enhancing Supply Chain Intelligence - Inside and Out
View More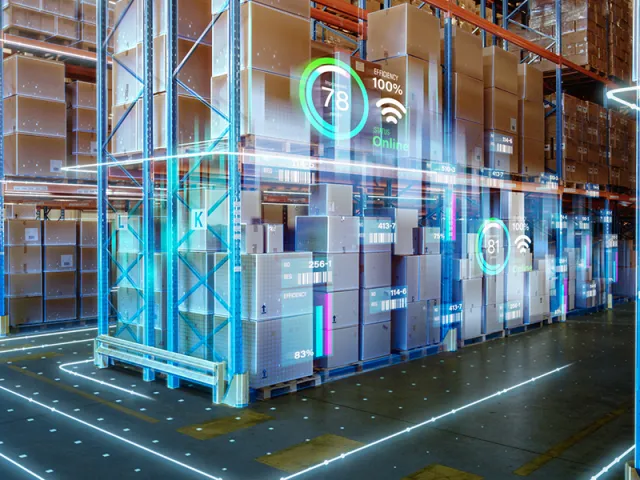
Video
Digitalizing Targeted Recall Notices for Real-Time Matching with DSCSA EPCIS Shipment Data
View More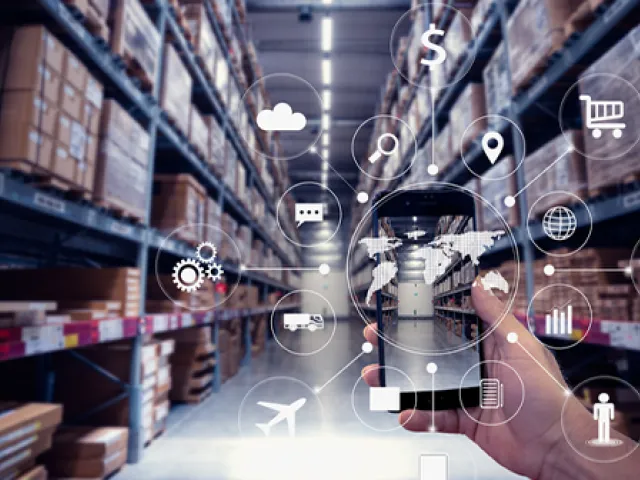
Video
Optimize Working Capital by Orchestrating Serialized Product Inventory Transactions and ASNs with Network Partners
View More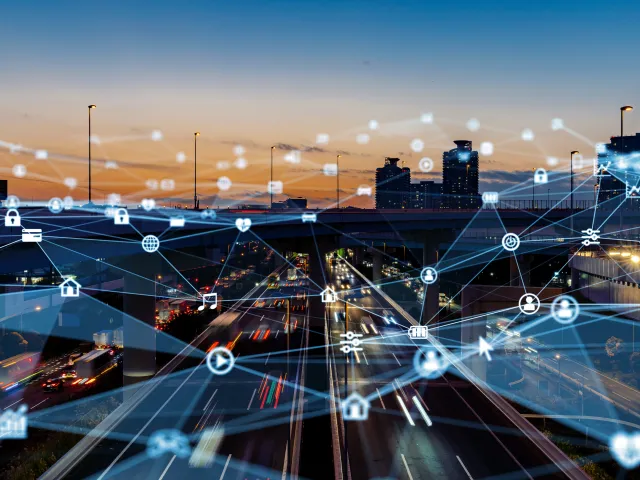
Video
Breaking Silos: Creating the Collaborative Corporate Foundation to Enable Supply Chain Orchestration
View More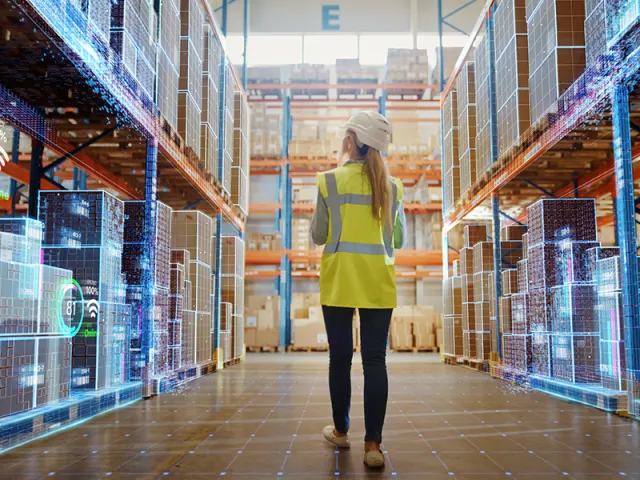
Video
Improve Chargeback Reconciliation With EPCIS, Serialized Product Data, and ASN and PO Transactions
View More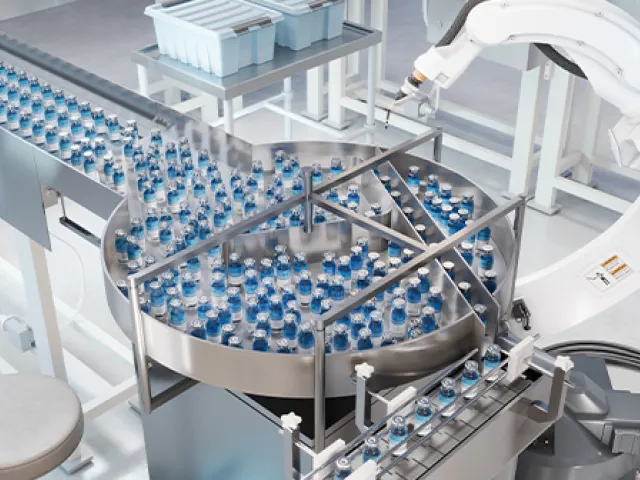
Video
Driving Business Predictability and Strategic Partnerships in CMO Networks by Leveraging DSCSA and Digitalization
View More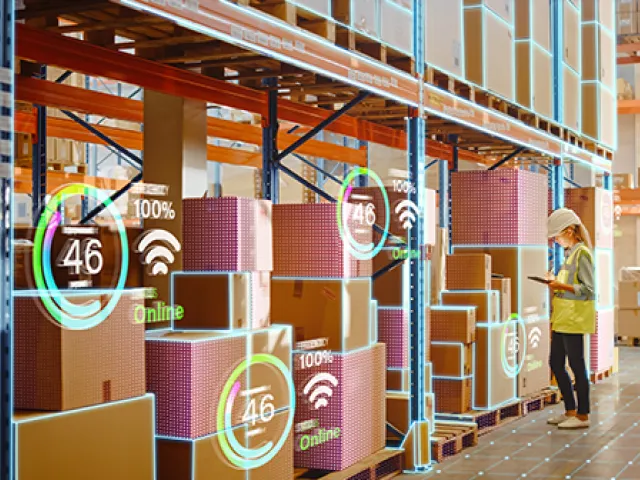
Video